Content
Brief Introduction of Water Jet Glass Cutting
Water jet glass cutting is an effective method. Waterjet cutting can produce precise cuts in glass with minimal chipping, cracking, or other damage.
In waterjet cutting, a high-pressure stream of water is directed at the glass, often with added abrasives such as garnet. The waterjet stream can cut through the glass quickly and accurately, producing clean edges and precise shapes.
Water jet glass cutting is often used in the glass industry for a variety of applications, such as architectural glass, decorative glass, and automotive glass. Water jet glass cutting can also be used to cut holes and notches in glass for hardware installations, as well as to create intricate designs and patterns in glass.
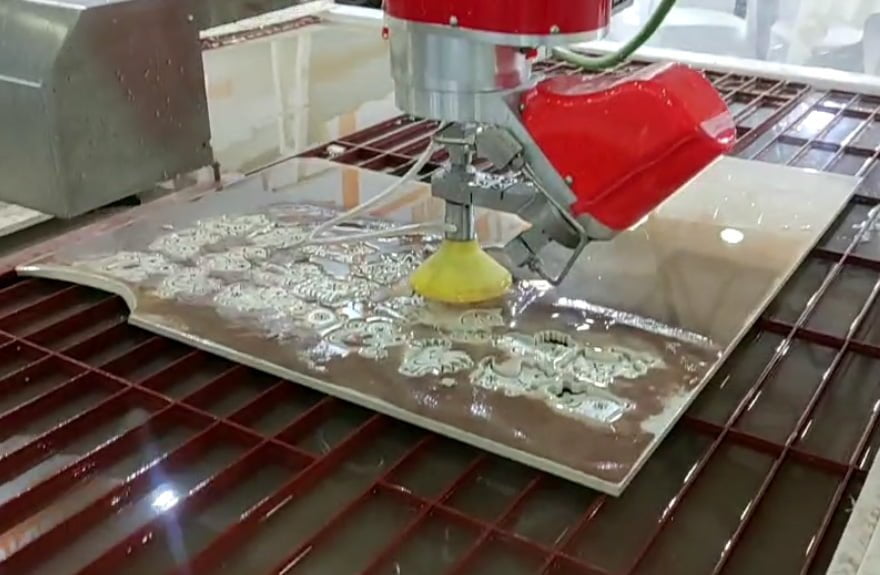
Advantages of Water Jet Glass Cutting
1. Types of glass
Water jet glass cutting can be used to cut various types of glass, comprising tempered glass, laminated glass, and annealed glass. However, the cutting process may differ resting with the type of glass being cut.
2. Cutting thickness
Water jet glass cutting can be used to cut glass of varying thicknesses. However, the thickness of the glass being cut can affect the cutting speed and the type of abrasive that should be used.
3. Edge quality
Water jet glass cutting can produce high-quality cuts in glass with minimal chipping, cracking, or other damage. However, the edge quality of the cut can be affected by factors such as the cutting speed, the angle of the waterjet stream, and the type of abrasive that is used.
4. Design flexibility
Water jet glass cutting can be used to create a wide range of shapes and designs in glass. The flexibility of the cutting process allows for the creation of intricate and complex designs, as well as the ability to cut holes and notches in glass for hardware installations.
5. Environmental impact
Water jet glass cutting is an environmentally friendly cutting method that does not produce any hazardous fumes or waste. The abrasive waste can be disposed of safely.
Overall, water jet glass cutting is a versatile and effective method that can produce high-quality cuts with minimal damage or waste.
Differences in Water Jet Glass Cutting Process for Each Type
1. Laminated glass
Laminated glass is a type of safety glass that is constitutive of two or more layers of glass bonded together with a layer of polyvinyl butyral (PVB) interlayer. Laminated glass is designed to remain intact even if it is broken.
When cutting laminated glass, it is important to use a waterjet with a high-pressure stream and a low-abrasive nozzle to prevent damage to the interlayer. The cutting process typically involves cutting through one layer of glass at a time and then separating the layers using a heat or chemical process. After the glass is cut, the edges can be finished using a grinding or polishing process.
2. Annealed glass
Annealed glass is the most common sort of glass and is often used in windows, mirrors, and other applications. It is cooled slowly to relieve internal stresses and improve its strength and durability.
When cutting annealed glass, a waterjet with a high-pressure stream and a high-abrasive nozzle can be used to achieve a fast and precise cut. The cutting process typically involves cutting through the glass in a single pass and then finishing the edges using a grinding or polishing process. To avoid chipping or cracking the edges of the glass, the waterjet should be angled slightly away from the edges of the glass during the cutting process.
3. Tempered glass
After our experiment, water jet glass cutting can not be used to cut tempered glass at present, otherwise it will lead to the breakage of tempered glass.
It is important to use the appropriate water jet glass cutting process and techniques for each type to ensure a high-quality and safe cut.
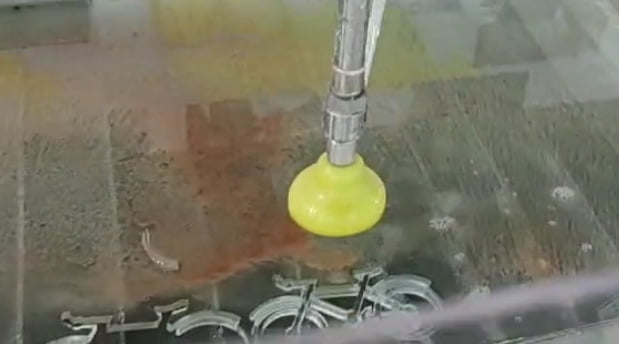
Precautions of Water Jet Glass Cutting Should Be Taken
Water jet glass cutting can be a precise and efficient process if done exactly. However, there are some key precautions and common mistakes that should be paid attention to ensure a high-quality and safe cut.
1. Wear protective gear
During the process of water jet glass cutting, it is important to wear protective gear to prevent injury. Safety glasses ought to be worn to protect the eyes from flying glass shards and water. Gloves should be worn to protect the hands from cuts and abrasions. A protective apron can also be worn to protect the body from water and debris.
2. Secure the glass
The glass should be securely positioned and supported during the water jet glass cutting process to prevent it from moving or vibrating, which can cause damage or injury. Securing and supporting glass properly during waterjet cutting is crucial to ensure a successful, high-quality cut and to prevent damage to the glass or injury to the operator.
Here are some best practices during the process of water jet glass cutting:
a. Use appropriate fixtures
Use appropriate fixtures, such as clamps or magnets, to secure the glass in place during cutting. The fixtures should be designed to prevent the glass from moving or vibrating during the water jet glass cutting process.
b. Use appropriate padding
Use appropriate padding, such as foam or rubber, between the glass and the fixtures to prevent the glass from being scratched or damaged. The padding should also help to absorb any vibration during cutting.
c. Check for flatness
Check the glass for flatness before securing it in place. If the glass is not flat, it may need to be shimmed to ensure that it is properly supported during cutting.
d. Avoid over-tightening
Avoid over-tightening the fixtures, as this can cause the glass to crack or become damaged. The fixtures should be tightened just enough to hold the glass securely in place.
e. Use proper spacing
Use proper spacing between the glass and the fixtures to ensure that the waterjet stream can access the entire surface of the glass being cut.
f. Check for obstructions
Check for any obstructions or debris that may interfere with the water jet glass cutting process or cause damage to the glass. Remove any obstructions or debris before beginning the water jet glass cutting process.
3. Using the suitable abrasive
The type and size of abrasive used in the water jet glass cutting process can affect the quality of the cut. Using the incorrect abrasive can cause damage to the glass, such as chipping or cracking. It is important to use the appropriate abrasive for the type of glass being cut and to adjust the abrasive flow rate as needed to achieve the desired cutting quality.
4. Use the appropriate cutting settings
The cutting speed can have a significant influence on the edge quality of the glass. Cutting glass too quickly or too slowly can result in different types of edge quality issues.
If the cutting speed is too fast, the waterjet stream may not have enough time to fully penetrate the glass, resulting in a rough or jagged edge. This can also cause the glass to crack or chip, especially if the glass is thin or brittle. In some cases, the glass may even be completely severed, resulting in a poor quality cut with uneven edges that may require additional finishing.
On the other hand, if the cutting speed is too slow, the waterjet stream may create a wider kerf, or cutting width, than necessary. This can issue in a loss of material and a longer cutting time. The slower cutting speed can also cause the glass to heat up, which can lead to thermal stress and cracking.
To achieve the best edge quality during water jet glass cutting, it is important to find the right balance between cutting speed and cutting quality. The cutting speed should be adjusted based on the thickness and type of glass being cut, as well as the desired edge quality.
While cutting speed is an important factor in achieving good edge quality, other factors such as the waterjet pressure, nozzle diameter, and abrasive flow rate can also have an impact. For example, increasing the waterjet pressure can help to improve the edge quality by increasing the amount of energy delivered to the glass. Similarly, using a smaller nozzle diameter can help to increase the cutting speed while maintaining good edge quality.
Using the incorrect settings can cause the glass to crack, chip, or shatter. It is important to refer to our manufacturer’s instructions or consult with us to determine the appropriate settings for cutting glass.
5. Use a low-abrasive nozzle
When cutting laminated glass, a low-abrasive nozzle should be used to prevent damage to the interlayer. When finishing the edges of tempered glass, a low-abrasive nozzle can also be used to avoid chipping or cracking the edges.
6. Correct nozzle angle
The angle of the waterjet nozzle can affect the quality of the cut. If the nozzle is angled too steeply, it can cause the glass to crack or chip. It is important to use the appropriate nozzle angle for the type of glass being cut and to adjust the angle as needed.
7. Keep the water jet glass cutting area clean
The area around the waterjet glass cutting machine should be kept clean and free of debris to prevent injury. Any spills or debris must be cleaned up promptly.
8. Properly drying the glass
Glass that is not properly dried after cutting can become damaged or corroded. It is important to properly dry the glass after cutting and to store it in a dry and clean location.
By following these safety precautions, the quality of the glass cut can be improved and the risk of injury or damage during the water jet glass cutting process can be minimized. It is also critical to receive proper training and instruction on how to safely operate the waterjet cutting machine before attempting to cut glass or any other materials.
Water Jet Glass Cutting Exhibition
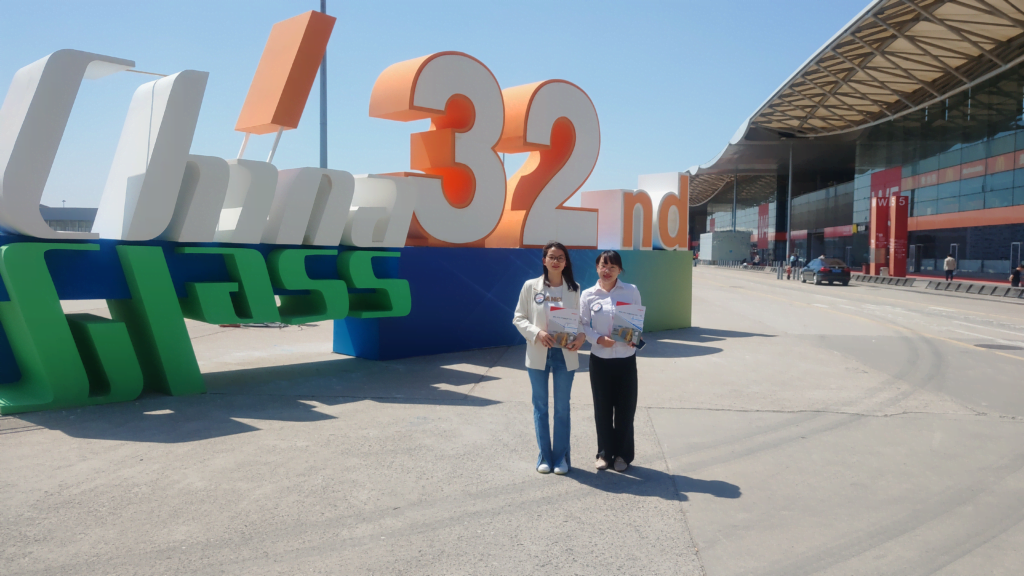
From May 6th to 9th, 2023, our company participated in the 32nd China International Glass Industrial Technical Exhibition. At the exhibition, we introduced the technology and machine of Win-Win Waterjet Company and explained the principle, advantages and operation process of water jet glass cutting to the participants of glass related industries from various countries.
Water jet glass cutting technology now is widely used in the glass industry, if you have the need to cut glass, welcome to contact us for communication and order!
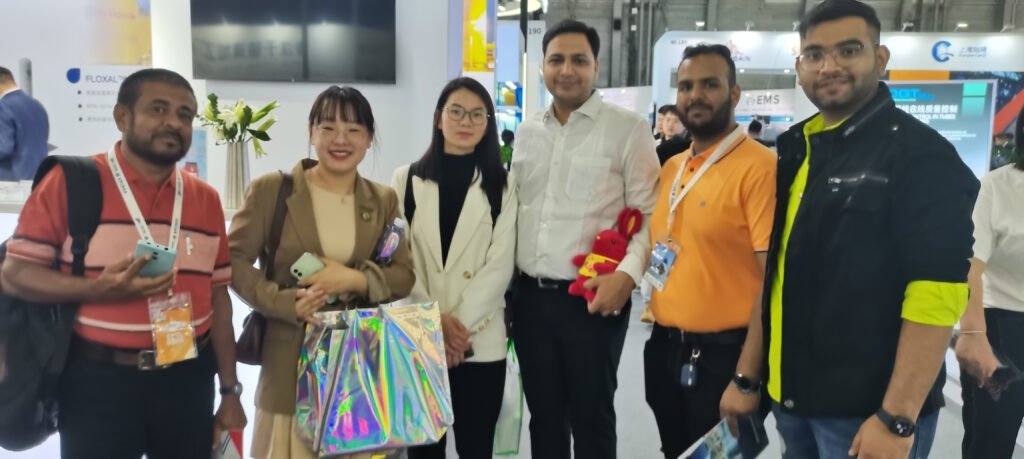